On to the topic, let’s take a look at what this 2.5-generation mask captain looks like:

It can be seen that compared with the original mask machine, the changes are still a little big. Overall, this mask machine combines the original advantages and draws on other mask machines (such as the N95 mask machine mentioned last time). The advantage is that the floor area becomes smaller and the production is more stable. Many of these institutions are ingenious and worthy of our study, so let’s get into the topic and start to analyze the principles of this mask machine and the institutions worth studying from beginning to end.
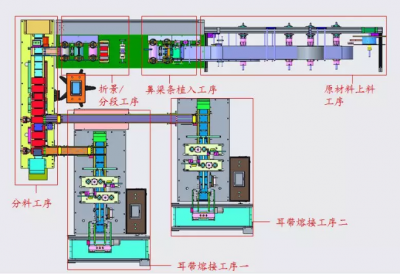
First of all, this mask machine produces external ear band masks (that is, the ear bands face outward).
→ The cloth is cut from the raw material feeding process through the implantation process of the nasal bridge strip, and the nasal bridge strip is cut and implanted in the mask, and at the same time, the ultrasonic welding machine is used to emboss the longitudinal sides of the outlet mask;
→ Then go through the scene folding / segmentation process, fold the three folds on the mask, and emboss the two sides of the mask horizontally by an ultrasonic welding machine, while cutting the mask in sections;
→ The segmented mask enters the material distribution process, and then is divided into earband welding process 1 and earband welding process 2;
→ The mask is welded to the mask through the welding process of the ear band, and then output to the feeding conveyor.
The above is the overall working sequence of this 2.5-generation mask machine. Let’s start analyzing each process in turn.
01 Raw material feeding process

It can be seen that this mask machine also has four cloth roll racks, which can also be used as four-layer disposable masks. The rightmost side is the nose bridge line rack.
After the cloth is rolled out of the cloth, it passes through the respective cloth passing rollers, and finally goes out of the cloth support frame to enter the next process; the nose bridge line comes out of the placing rack, and enters the next process through the reel.
Then, let’s analyze these organizations:
1. Cloth roll rack:

About the cloth roll fixing block: its role is to insert from the two ends of the central hole of the cloth roll to form a main body, and then fix the cloth roll fixing block on the rotating shaft through the star handle;
Damping mechanism: As for the role of the damping mechanism, as mentioned in the previous article, it is not a problem. This damping mechanism looks a lot simpler than the original one, but the principle is still the same: the fixed seat passes the spring to damp the damping. The block is pressed against the rotating shaft and plays a damping role.
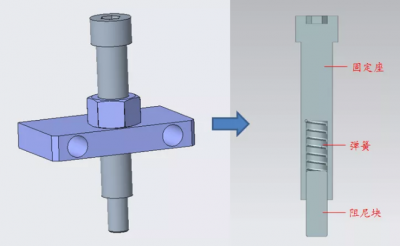
Everyone must have found out that the entire structure is different from the previous mask machine. The left and right position adjustment mechanism of the fabric roll is missing. In fact, there are no adjustment mechanisms, but they are different from the original. Let ’s talk about this adjustment below. mechanism.
Handwheel + screw + screw holder + screw nut holder + adjustment seat + adjustment plate + limit mechanism + bearing fixing mechanism, this set constitutes the left and right adjustment mechanism of the cloth roll;
First of all, let ’s take a look at the bearing fixing mechanism. If we only look at this place, the adjustment plate can be rotated forward, backward, left, and right. At this time, the limit mechanism plays a role of restricting the left and right rotation of the adjustment plate, and the lower adjustment seat also limits the front and back of the adjustment plate The effect of rotation, so that the adjustment plate is restricted, and will follow the adjustment seat to move back and forth.
I guess the reason for doing so complicated is to avoid the mechanism being stuck due to the inaccurate installation position. (Just a personal guess, if anyone knows the real reason, welcome to add in the comment area)
Take a look at its adjustment principle:
Turning the hand wheel drives the screw rod to rotate → Since the screw nut seat is fixed, the screw rod will advance or retreat with the rotation of the hand wheel → The screw rod will also drive the adjustment seat, the adjustment plate and the bearing fixing mechanism forward or backward → bearing fixing The seat mechanism drives the rotary shaft forward or backward, so as to adjust the left and right positions of the cloth roll (Note: the bearing fixing mechanism is fixed on the rotary shaft by screws)
Nose bridge placement rack
After reading the previous N95 mask machine analysis article, you should know that this organization has already analyzed it once, so I will not repeat it. If there are interested students, you can go to the public account to find an article about N95 mask machine analysis. , Which contains a detailed analysis of this institution.
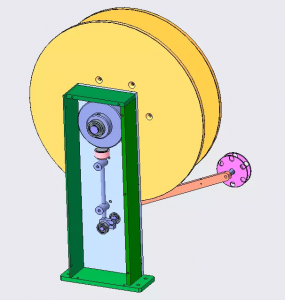
3. Cloth support
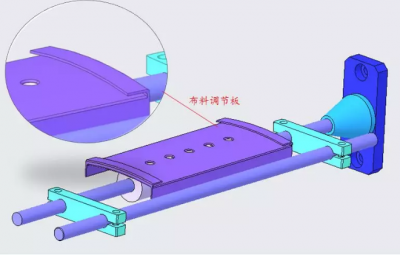
This mechanism is different from the original one with a cloth adjustment plate. We can see that the two ends of the adjustment plate are folded sheet metal, and the cloth is passed through the sheet metal folded from both sides, so its function can be Prevent the fabric from moving around.
OK, the raw material loading process is analyzed, and the next step is entered.
02 Nose bridge strip implantation process, folding / segmentation process
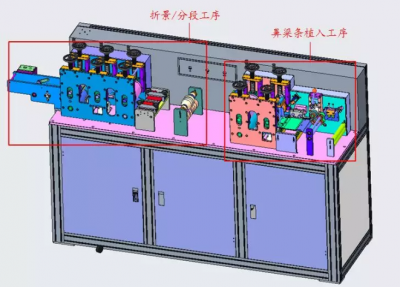
Let’s first understand the specific working order and mechanism of the two processes.
1. Nasal bridge implantation process
It is said that the nasal bridge implantation process actually includes the process of longitudinally embossing the pressure outlet cover. See the following figure for details:
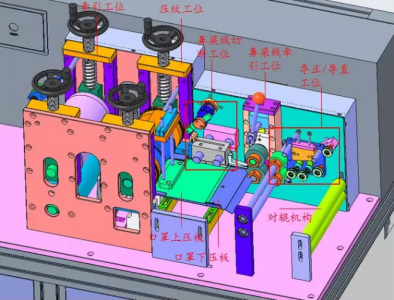
The working sequence is:
→ The fabric passes through the middle of the roller mechanism and enters between the upper and lower pressure plates of the mask; at the same time, the nose bridge line passes through the straightening / straightening station, enters the nose bridge line traction station, and finally the nose bridge line is fixed by the cutting station. Cut off the length and enter the embossing station with the mask;
→ From the traction station, the mask is pulled into the next process.
Let’s analyze the organization in the process:
First of all, there is nothing to say about the roller mechanism, that is, the two rollers, and the height is also manually adjusted through the long circular holes on both sides. (This mechanism does not have the roller adjustment mechanism of the N95 mask machine for easy adjustment)
1) Straightening / straightening station
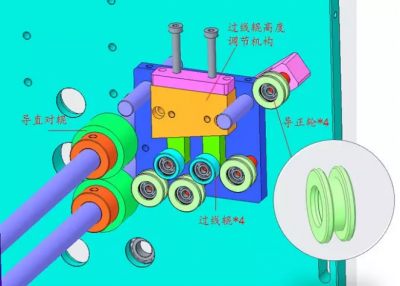
The function of this mechanism is to straighten and straighten the nose bridge line. The nose bridge line passes through 4 guide wheels and 2 wire passing rollers, passes through the middle of the guide rollers, and enters the rear traction station. (Note: Straightening is unpowered to the roller)
Let’s take a look at the height adjustment mechanism of the thread passing roller:

The adjusting block is installed on the fixed seat. It can be seen that the adjusting screw and the thread passing roller mounting seat are dovetail grooves. When the adjusting screw is screwed, the thread passing roller mounting seat can be moved to achieve the purpose of adjusting the height of the thread passing roller. .
2) Nose bridge line traction station

First of all, you need to know that the sliding seat drives the lower sliding block adjustment mechanism, the traction wheel slide block and the upper traction wheel to move together. Regarding the principle of the vertical adjustment of the sliding seat, I actually talked about it on the previous net red mask machine. Copy it over, the principle is the same:
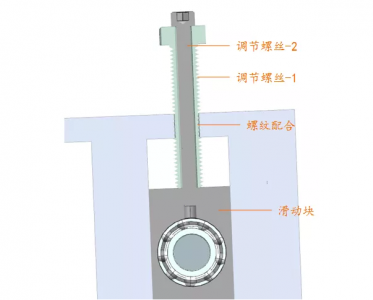
The adjusting screw-1 is a hollow screw. The adjusting screw-2 and the sliding block are threaded. The adjustment process: The adjusting screw-2 is locked on the sliding block, but be careful not to lock it. At this time, turn the adjusting screw-1 (pay attention to keep the adjustment The screw-2 does not turn), the slide block can be moved up and down. After adjusting to the appropriate position, tighten the adjustment screw-2 and it is OK.
The function of the adjustment of the sliding block of the traction wheel is: when changing the nose bridge line, put the nose bridge line between the upper and lower traction wheels again, and then look at the adjustment principle of the sliding block of the traction wheel:
The adjustment handle is driven to drive the connection block 1 to rotate, and the connection block 1 drives the connection block 2 to move, so that the traction wheel sliding block and the upper traction wheel are moved upward or downward to achieve the purpose of adjustment.
Note: The upper traction wheel is a non-powered wheel; the power is driven by the lower traction wheel, and it is intermittently driven. The power transmission will be analyzed in detail later.
3) Nose bridge cutting station

As can be seen from the above figure, there are cloth pre-folded sheet metal and hemming sheet metal on both sides of the lower platen of the mask. When the cloth passes the pre-folded sheet metal, the two sides of the cloth are folded to approximately 90 °; , Fold the fabric down to 180 °.
The nose bridge line enters the cutting mechanism from the entrance, the rotary balance wheel rotates once, and the nose bridge line is cut once according to a fixed length, and the front nose bridge line traction station is connected. The working sequence is this:
→ The nose bridge line traction station rotates once intermittently, and the nose bridge line is taken forward for a while. After the stop, the balance wheel is used to strike the cutter once to cut the nose bridge line.
→ After cutting, the nose bridge line enters the folded fabric from the pipe, and then enters the embossing station together.
After publishing the analysis article of the N95 mask machine, someone personally wrote to me and asked for a detailed analysis of the nose bridge cutting mechanism. This time, I used this mask machine to analyze the working principle of the cutting mechanism:
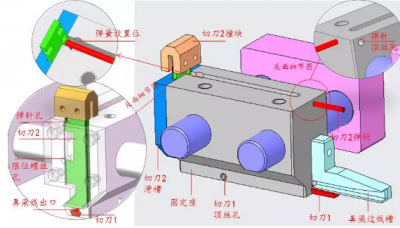
The first thing to know is: the nose bridge line enters through the wire slot and exits from the exit; the cutter 2 spring needle is inserted into the spring needle hole; there is a spring in the spring placement position, which is located below the spring needle; Limit screws to ensure that the cutter 2 will not be ejected.
Then look at how it works:
Rotating balance wheel hits the cutter 2 and hits the block → Cutter 2 goes down, cuts the nose bridge line with the cutter 1, and at the same time bends the spring pin down, compressing the spring With the spring force, lift the cutter 2 upwards until it stops after touching the stop screw and returns to its original position.
The above is the principle of the cutting mechanism. Even if these stations are analyzed, continue to analyze the embossing station and the cloth traction station.
4) Embossing station
Let’s talk about the role of these two stations first:
Embossing station: the embossing on both sides of the longitudinal direction of the embossing cover; traction station: pressing the fabric to provide driving force for the forward movement of the fabric.
Look at the detailed picture again:

Regarding the ultrasonic vibrator / welding head, it will not be explained here. If you are interested, you can take a look at the first mask machine analysis article;
Then talk about the adjustment mechanism of the two stations:
The inside of the adjusting screw is hollow, and the screw and the guide shaft are slidingly matched;
First adjust the height of the bearing with the seat by the screws on the adjusting block → Then turn the handwheel to adjust the adjusting screw downwards, but be careful not to hold the adjusting screw against the guide shaft, so that the belt seat can be pressed by spring force Bearings.
The principle of the adjustment mechanism of the traction station and the embossing station is the same, except that there is no adjustment block under the traction station, and the spring directly presses the upper roller on the lower roller.
The advantage of the adjustment mechanism is that the fabric can be continuously subjected to downforce.
2.Folding / Segmentation
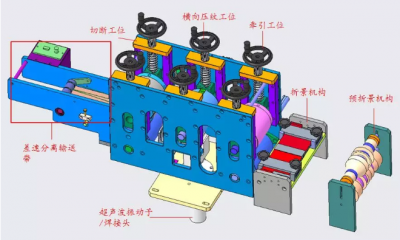
1) The functions of the pre-folding mechanism and the folding-folding mechanism are actually to fold the folds on the hood, directly on the actual production photos, and see more clearly:

2) Traction station, transverse embossing station, cutting station
The adjustment mechanisms of the three stations have been described before, so here is the role of them.
Traction station: presses the fabric to provide driving force for the forward movement of the fabric; transverse embossing station: presses the outlet cover laterally;
Cutting station: Cut the mask according to a fixed length.
3) Differential speed separation conveyor
The role of the differential separation conveyor belt: Because the front mask bodies are continuous, if you do not separate the gaps, the rear can not be divided. Therefore, when using this conveyor belt, you can use the speed difference to pull the front and rear mask bodies apart gap.
3.Power transmission of nose bridge implantation process and folding / segmentation process
The mechanisms of these two processes have been analyzed. Let’s take a look at their power transmission.
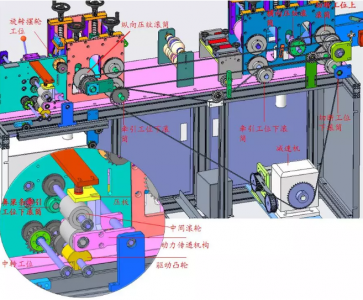
It can be seen that the power of the two processes comes from the following motor + reducer. The type of reducer is worm gear and worm, and the following is the internal structure diagram:

Then look at power transmission:
① The reducer transmits power to the lower roller of the cutting station and the lower roller of the two traction stations;
② The lower roller of the cutting station cooperates with the gear to transmit power to the upper roller of the cutting station;
③ Cut off the two sprocket wheels on the roller shaft at the station, and transmit the power to the horizontal embossing roller and the vertical embossing roller respectively;
④ The sprocket on the longitudinal embossing roller transmits power to the driving cam, and the driving cam power is used to drive the nose bridge traction station;
⑤ The gear on the driving camshaft transmits power to the intermediate station, and the sprocket on the intermediate station finally transmits the power to the rotary balance station.
The above is the complete power transmission process of the two processes. Let’s take a look at the working principle of the driving cam driving the nose bridge traction station:
The driving cam rotates, and each time it reaches the cam surface, it will push up the power transmission mechanism to contact the middle roller. At this time, the power of the driving cam will be transmitted to the middle roller, and the gear on the middle roller shaft will transmit the power to the nose bridge bar. Lower roller in traction station;
When the cam surface passes, the power transmission mechanism will drop. At this time, the power transmission of the driving cam and the intermediate roller will be disconnected, and at the same time, the pressure plate will be depressed to stop the intermediate roller.
From the above working principle, it can be seen that the bottom roller of the traction station of the nose bridge strip is rotated intermittently, and the nose bridge strip advances accordingly.
Some people may ask, why do we have to build such a complicated mechanism at the station that drives the bridge of the nose?
The reason why it is so complicated is to add a “brake function”. Without this function, each time the drive cam drives the middle roller, the middle roller will have an inertia, and this inertia will cause the length of the nose bridge to advance every time Inconsistent, so the role of this “brake function” is to stop the middle roller in time after the cam is driven.